Vektrex thermal measurement systems provide the tools needed for semiconductor device manufacturers and designers using the devices. Included Vektrex Thermal Measurement Software.
Vektrex V0331-4 Thermal Measurement SMU
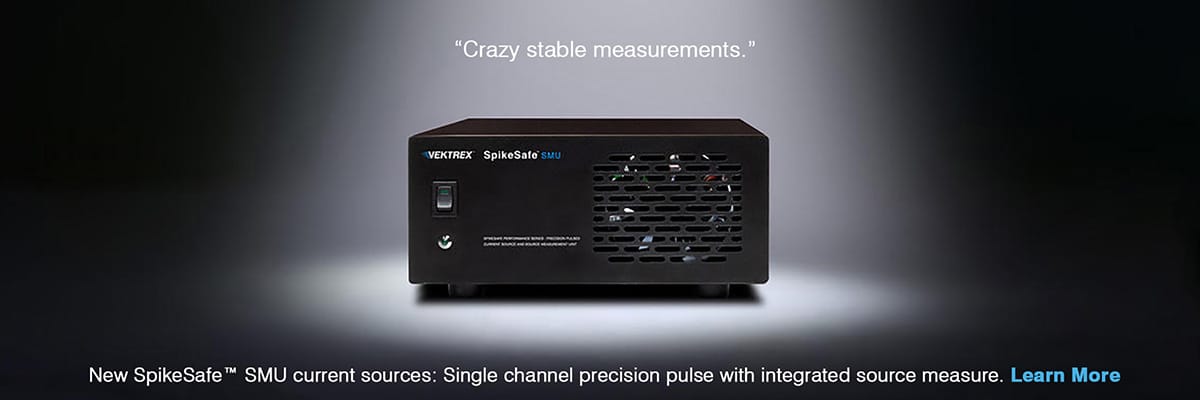
- JESD51 Dual Source model
- DC and pulse modes
- 300W total output power DC
- 1600W total output power pulse mode
- 100V maximum compliance voltage
- 4A maximum current (heating source)
- 10V / 100V / 400V ranges
- Includes Thermal Measurement Software
Vektrex Series 0331 Product Overview
The Vektrex Series 0331 is designed specifically for thermal measurement applications that demand tightly coupled sources and measurement. This SMU used for junction temperature measurement based upon the JEDEC Electrical Test Method integrates two highly stable current sources and a single true differential digitizer. The two current sources work in tandem to measure Vf at heating and cooling currents with a transition time <50us. The true differential digitizer provides extremely precise measurement capabilities with detection of mV changes – important when measuring junction temperature. This is a compact, single channel, DC and pulsed tester. Manufacturers of LEDs and semiconductor devices, luminaires and end user modules for UV disinfection, semiconductor, automotive and medical industries will find Series 0331 SMU units invaluable for wide range of thermal measurement, characterization and production test applications.
Key Features
- Power of three instruments in one (IV source, Bias source, Digitizer)
- 300W total output power
- Standard SCPI interfaces
- Vektrex Thermal Measurement Software for Junction Temperature, Thermal Resistance and Transient Thermal Impedance Test
- CE / RoHS
- 89mm (H) x 213mm (W) x 370mm (D) dimension, 3.21kg weight
Other Thermal Measurement SMU
- V0331-05 – 500mA maximum current; 200W total output power
- V0331-5 – 5A maximum current; 600W total output power; 1,600W pulsed output power
- V0331-10 – 10A maximum current; 600W total output power DC mode; 1,350W pulsed output power
Junction Temperature Measurements for Luminaire Manufacturers
- Junction Temperature (Tj) has a direct impact on the long-term reliability of a laser or LED. Higher in-situ Tj reduces long-term reliability.
- Quantitively determine the LED/device junction temperature ‘in-situ” for the application. This information is useful for products today and the future when there is a need to validate next generation LEDs.
- Tj also impacts the operating characteristics of LEDs and lasers. For example, an amber LED’s light output decreases dramatically as junction temperature increases.
- Using the JEDEC Electrical Test method, the LED is being directly measured. LED/device manufacturers cannot argue with this data.
- Reduce R&D cycles. The data on LED datasheets is not always accurate or complete. With Vektrex thermal measurements validation is possible
- LED manufacturers typically provide performance specifications at a specific Tj along with derating factors that allow performance at other temperatures to be calculated. Using these values, along with actual in-situ measurements, product designers verify the product will perform within its advertised specifications.
- Tune torque, heatsinks and thermal interface material.